In the intricate world of aviation, the heartbeat of any aircraft lies within its electrical systems.
These systems are the lifelines that power everything from the smallest cockpit indicators to the most complex in-flight entertainment systems. Beyond merely turning on lights or initiating the ignition, aircraft electrical systems are sophisticated networks that ensure the seamless operation and safety of the aircraft in the skies.
Comprising Direct Current (DC) Systems, Alternating Current (AC) Systems, and the versatile Combination AC/DC Systems, each plays a pivotal role in catering to the unique demands of different types of aircraft.
From the simplicity of single-engine planes to the complexity of jumbo jets, understanding these electrical systems opens a window into the technological marvels that make modern flight possible.
Join us as we delve into the electrifying world of aircraft electrical systems, where every wire and switch carries the weight of human ingenuity and the spirit of exploration.
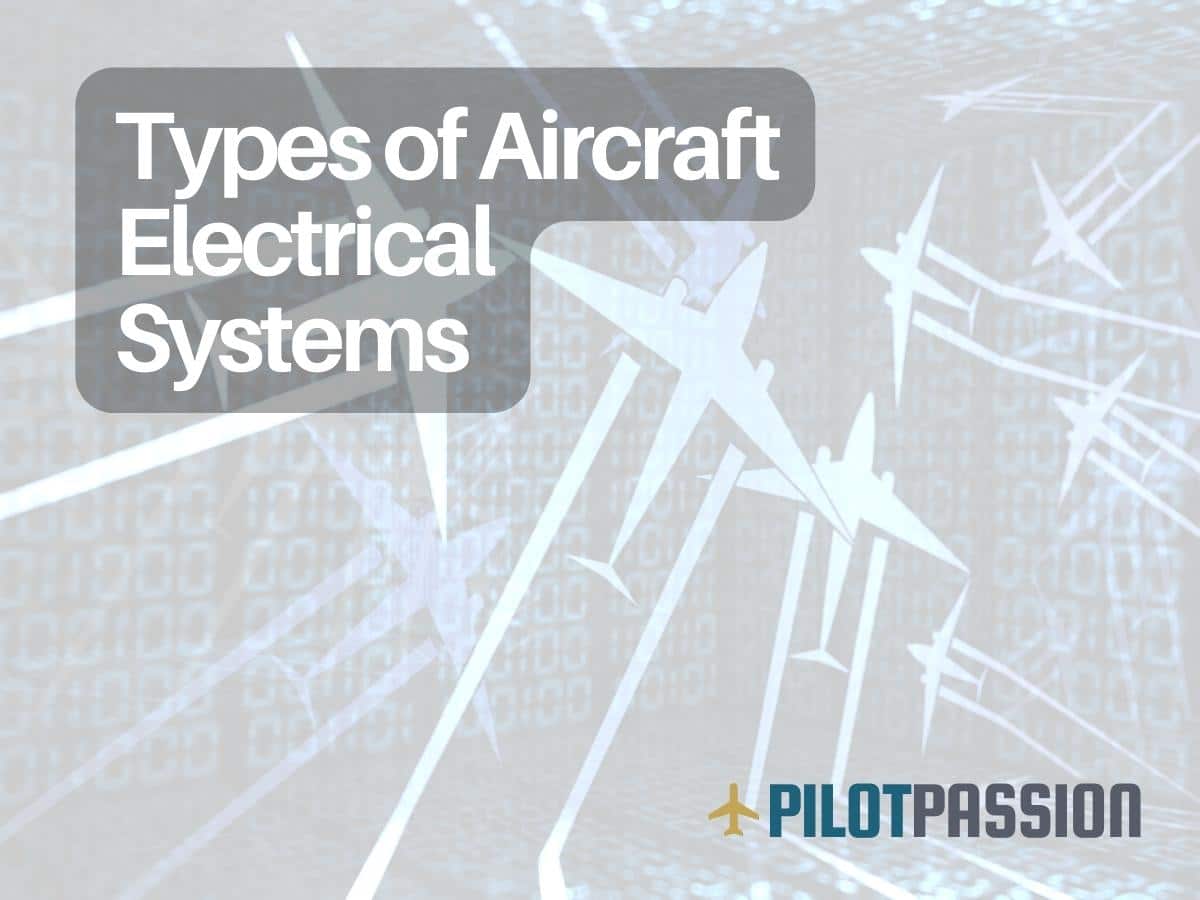
Table of Contents
Aircraft Electrical System Fundamentals
Aircraft electrical systems are essential for powering various components and systems on board. These systems are generally divided into three types:
- Direct Current (DC) Systems
- Alternating Current (AC) Systems
- Combination AC/DC Systems.
Direct Current (DC) Systems
Direct Current (DC) Systems are commonly found in smaller aircraft and provide power in the form of a constant voltage and current. The main components of a DC system include:
- Battery: Provides initial power to the system when the engine is not running.
- Generator or alternator: Runs off the engine and supplies continuous power while the engine is operating. Some aircraft may use hydraulic motors or Ram Air Turbines (RAT) as an alternative power source.
- Voltage regulator: Ensures a stable output voltage.
- Distribution system: Transfers electrical power to various aircraft systems and components.
The typical voltage output for DC systems is around 28V.
Alternating Current (AC) Systems
Alternating Current (AC) Systems are more commonly found on larger, more complex aircraft. These systems provide power as a constantly changing electrical current.
AC systems have several advantages over DC systems, such as the ability to transmit power over long distances with minimal losses and the ease of use with motors and transformers.
The main components of an AC system include:
- Generator or alternator: Engine-driven and produces power at a specific frequency, usually 400 Hz.
- Transformer-rectifier: Converts AC power to DC power for specific aircraft components.
- Inverter: Converts DC power to AC power if required.
- Distribution system: Transfers electrical power to various aircraft systems and components.
In an aircraft AC system, the line voltage is about 200 volts, and the phase voltage is about 115 volts.
Combination AC/DC Systems
Many modern aircraft utilize a combination of both AC and DC systems. This approach offers the flexibility and advantages of both systems, allowing for a more efficient and reliable electrical system.
In these systems, power is generated through a combination of engine-driven generators or alternators and other power sources like APUs or hydraulic motors. The distribution system is designed to transfer power between AC and DC components as needed, ensuring optimal performance of the aircraft’s electrical systems.
Aircraft DC Systems
Aircraft DC systems play a critical role in powering various flight instruments, controls, and switches that are essential for safe and functional operation.
DC Generators
DC generators are engine-driven devices that convert mechanical energy into direct current electrical power by leveraging the principle of electromagnetic induction. They are commonly used in smaller aircraft, and their output typically ranges from 14 to 28 volts DC.
DC generators are known for their reliability and simplicity in design, which makes them a popular choice for aircraft electrical systems. They are gradually being replaced by alternators due to the latter’s increased efficiency and lower maintenance requirements.
Batteries
The lead-acid or nickel-cadmium aircraft battery serves several functions in a DC system, such as providing power for engine starting and ground operations, acting as a backup energy source during emergency situations, and supplying power to various avionics and lighting systems.
It’s really important to monitor the battery’s condition and maintain it at its optimal operating capacity, ensuring adequate power is available when needed.
Circuit Breakers and Fuses
Safety is paramount in aircraft electrical systems, and one of the most effective safety components is the use of circuit breakers and fuses.
Circuit breakers are electromechanical switches that automatically interrupt electrical flow whenever they detect an abnormal current, preventing potential damage and failure. They can be manually reset once a fault has been corrected, making them a reusable safety device.
Fuses, on the other hand, are single-use components that provide a similar protective function. When a fuse detects an abnormal current, it melts internally and breaks the electrical circuit, safeguarding other system components from damage.
In most aircraft, fuses are gradually being replaced with circuit breakers due to their resettable nature and enhanced reliability.
Aircraft AC Systems
Aircraft AC systems are critical for powering various essential components and equipment on modern aircraft.
AC Generators and Alternators
AC generators, also known as alternators, are responsible for producing electricity in aircraft. They are usually engine-driven, but can also be powered by an Auxiliary Power Unit (APU), a hydraulic motor, or a Ram Air Turbine (RAT). The typical generator output for aircraft is around 115-120V/400Hz AC.
Alternators differ from DC generators in that they produce alternating current (AC) instead of direct current (DC). They typically have a high number of poles to generate the required high frequency (400Hz), which makes them more efficient and lightweight compared to their DC counterparts.
Rectifiers and Inverters
Rectifiers and inverters are essential components of aircraft electrical systems, responsible for converting AC power to DC power and vice versa.
Rectifiers are used to convert high-voltage AC power into lower-voltage DC power using transformer rectifier units (TRUs), which are typically designed in a 12-pulse configuration. This conversion is important as both AC and DC power are required to operate various systems on the aircraft.
On the other hand, inverters are used to convert the DC power generated by the battery or other DC sources back into AC power, which may be necessary for operating specific components or devices within the aircraft that require AC input.
Frequency Management
Managing the frequency of the AC power in an aircraft’s electrical system is crucial for optimal performance and efficiency. The standard frequency for aircraft generators is 400Hz, which is considered the optimal frequency for efficient operation and reduced size and weight of electrical components.
Some aircraft employ frequency management techniques to ensure that their electrical systems maintain a constant frequency throughout the flight, regardless of fluctuations in engine speed or other factors. This can include devices such as frequency converters or frequency-control motors to help stabilize and regulate the output frequency and voltage.
Combination AC/DC Systems
Combination AC/DC electrical systems in aircraft are designed to take advantage of the benefits of both AC and DC power.
These systems typically employ a hybrid layout, allowing certain components to run on AC power while others use DC power. This section will discuss the hybrid system layout, as well as the advantages and disadvantages of combination AC/DC systems in aircraft.
Hybrid System Layout
In a combination AC/DC system, the aircraft’s generator or alternator is primarily responsible for generating AC power. Typically, the generator output is around 115-120V/400Hz AC, while DC power is supplied at a voltage level of 28V.
The AC power is then converted to DC power using rectifiers or power converters. This allows for a more efficient and flexible distribution of power among various electrical components and systems in the aircraft, such as avionics, lighting, and motors.
Advantages
There are several benefits to using a combination AC/DC electrical system:
- Flexibility: By providing both AC and DC power, combination systems can accommodate different types of loads, such as DC motors and AC-powered avionics.
- Efficiency: Converting AC to DC power allows for more efficient energy distribution, as losses due to resistance are minimized.
- Redundancy: Having multiple power sources (AC and DC) provides a backup in case one of the power sources fails, ensuring continued operation of critical systems.
Disadvantages
Despite the advantages, there are also some drawbacks to combination AC/DC electrical systems:
- Complexity: The hybrid layout can make the electrical system more complicated, leading to more challenging maintenance and troubleshooting.
- Weight: Combination systems can be heavier than their AC or DC counterparts due to the additional components, such as rectifiers and power converters.
- Cost: The increased complexity and additional components may lead to higher costs for production and maintenance.
By utilizing both AC and DC power, combination electrical systems provide a flexible and efficient solution for aircraft power distribution.
However, these systems may also introduce increased complexity, weight, and costs as trade-offs.
It’s important for designers and engineers to carefully consider the specific needs and requirements of the aircraft when choosing the most appropriate electrical system.
Power Distribution and Protection
Distribution Bus
Aircraft electrical systems utilize a distribution bus to efficiently distribute power to different equipment onboard. The distribution bus acts as a central connection point where power is split and routed to various components.
In many cases, the power distribution system is configured as a combination of AC and DC Systems, depending on the requirements of the specific aircraft. For instance, larger aircraft typically rely on AC power systems since they have a better power-to-weight ratio and are simpler in design.
A bus-bar is an essential component of the distribution bus system. It is a conductor used to make multiple connections to various electrical loads. This reduces wiring and minimizes power losses in the aircraft electrical system.
Some aircraft also have backup or auxiliary power sources, such as a Ground Power Unit (GPU), to provide additional redundancy and enhance the reliability of the electrical system.
Circuit Protection Devices
Circuit protection devices are critical components in aircraft electrical systems to safeguard equipment from damage due to excessive current, short circuit, or any electrical fault. Some commonly used circuit protection devices are:
- Circuit Breakers: These are electromechanical devices designed to open a circuit automatically in case of an overcurrent event. They can be reset either manually or automatically and are a popular choice for aircraft electrical systems due to their reusability and reliability.
- Fuses: Fuses are one-time-use devices that melt and disconnect the circuit when the current surpasses a predetermined threshold. While effective, fuses are generally not preferred in aircraft electrical systems due to the need for replacement after each opening event.
- Current Limiters: These devices provide overcurrent protection by limiting the amount of current flowing through a circuit. They maintain a constant voltage under normal operating conditions but progressively decrease the voltage when the current exceeds a specified limit.
Proper power distribution and protection are essential for the reliability and safety of an aircraft’s electrical system.
By employing a combination of distribution bus systems and circuit protection devices, aircraft can effectively manage and route power to its critical components while minimizing the potential for equipment damage due to electrical faults.
Additional Aircraft Electrical Components
In this section, we will discuss some essential electrical components found in aircraft systems, including starter motors, lights and radios, spark plugs, and fuel pumps.
Starter Motors
Starter motors are a key component of the aircraft’s electrical system as they help to initiate the engine startup process. There are two main types of starter motors: direct current (DC) and alternating current (AC).
The DC starter motor usually runs off of the aircraft’s battery, while the AC starter motor is powered by an alternator or generator. To ensure a smooth starting process, it is crucial that the starter motor’s switches, wiring, and connections are maintained correctly.
Lights and Radios
Lights and radios are essential components of the aircraft’s electrical systems. The lighting system typically consists of various types of lights, such as:
- Navigation lights
- Anti-collision lights
- Strobe lights
- Landing/taxi lights
- Interior and cabin lights
These lights are powered by the aircraft’s generators and controlled by switches within the cockpit. Radios, on the other hand, are vital for communication between the pilot, air traffic control, and other aircraft.
Radios in an aircraft require an uninterrupted power supply, usually provided by the aircraft’s battery or alternator, and often have backup systems in case of a primary power failure.
Spark Plugs and Fuel Pumps
Spark plugs are responsible for igniting the fuel-air mixture in the aircraft’s combustion chambers. These devices require a strong electrical voltage to produce the necessary spark for combustion. The spark plugs are powered by the airplane’s alternator or generator.
The aircraft’s fuel pumps also rely on the electrical system for proper operation. These pumps transfer fuel from the fuel tanks to the engine, and sometimes require additional electrical components such as pressure sensors and switches.
The fuel pump system depends on a reliable power supply, usually provided by the aircraft’s main electrical system, to ensure consistent performance and safety during flight.
Aircraft Battery Types
Aircraft electrical systems often use different types of batteries for various applications such as engine starting, ground power units, and maintaining electrical bus at a constant voltage. This section will discuss two common types of aircraft batteries: Lead-Acid Batteries and Nickel-Cadmium Batteries.
Lead-Acid Batteries
Lead-acid batteries are a widely used type of battery in light aircraft for engine starter motors and ground power units. They are known for their low cost and reliable performance. The basic components of a lead-acid battery are:
- Positive plates made of lead dioxide
- Negative plates made of metallic lead
- Electrolyte containing sulfuric acid and water
Some advantages of Lead-Acid Batteries include:
- Affordability: They are generally less expensive than other types of batteries
- Availability: They can be easily found and replaced
- Reliability: They have proven to be a reliable source of power for aircraft applications
However, lead-acid batteries also have some disadvantages:
- Weight: They are heavier compared to other types of batteries
- Maintenance: They require regular maintenance, such as electrolyte level checks and topping up with distilled water
Nickel-Cadmium Batteries
Nickel-Cadmium (NiCd) batteries are another common type of aircraft battery, often used in larger aircraft due to their durability and energy density. They generally consist of nickel hydroxide as the positive electrode and cadmium as the negative electrode, with an electrolyte of potassium hydroxide.
Some benefits of Nickel-Cadmium batteries include:
- Maintenance: They require less maintenance compared to lead-acid batteries
- Charge retention: They can hold a charge for a long time, making them suitable for long-term storage
- Durability: They are known for their resistance to extreme temperatures and proximity to smoke or fumes from the aircraft’s engine
On the other hand, Nickel-Cadmium batteries have some drawbacks:
- Cost: They are usually more expensive than lead-acid batteries
- Environmental concerns: Cadmium is a toxic metal, and its disposal must be handled carefully
Aircraft Generator Types
Aircraft electrical systems can be classified into DC systems, AC systems, or a combination of both. This section will discuss the types of generators used in these systems, including engine generators, hydraulic motor generators, auxiliary power units, and ram air turbine generators.
Engine Generators
Engine generators, which can be either, you guessed it, an AC generator or a DC generator, are widely used in aircraft electrical systems. These generators transform mechanical energy from the engine into electrical energy.
AC alternators are more common, while DC generators are typically found on light aircraft. The output of these generators varies, with common sizes being:
- 12 or 24 volts for DC systems
- 115-120V/400HZ AC, 28V DC for AC systems
Engine generators use armature windings and field windings in their construction, with the latter producing a magnetic field to induce current in the armature. Relays help control the generator’s output voltage and ensure stable operation.
Hydraulic Motor Generators
In some aircraft, a hydraulic motor can be used to drive a generator, producing electricity. These hydraulic motor generators provide an alternative source of power when engine generators are unavailable or not operating optimally.
Auxiliary Power Unit
Auxiliary Power Units (APUs) are small turbine engines typically found in larger commercial and military aircraft.
They serve as a supplementary power source and can be used to generate electricity when primary engine generators are not in use, usually during ground operations. APUs produce AC output for avionic systems and other aircraft components.
Ram Air Turbine Generator
A Ram Air Turbine (RAT) generator is an emergency power source that uses aerodynamic forces to produce electricity. The RAT is a small turbine that deploys into the airstream, using the airflow to spin its blades and drive a generator/alternator inside the aircraft.
This type of generator is typically employed during emergency situations when other power sources are unavailable, providing a reliable backup to maintain critical systems.
Challenges and Safety Concerns
Battery Fires and Fumes
One important issue with aircraft electrical systems is battery fires and fumes. This is particularly concerning when dealing with lithium-ion batteries, which are commonly used in modern aircraft.
These batteries can experience thermal runaway, a chemical reaction that causes the battery to heat up and potentially catch fire.
To address this risk, manufacturers have implemented various safety features. For example, an aircraft typically has a battery containment system to mitigate the effects of a potential fire.
It’s crucial to have proper ventilation to disperse any fumes that may arise from a battery event.
Circuit Overloads
Circuit overloads occur when the current in an electrical system exceeds its designed capacity, which could lead to damage to the circuit breaker, its wiring, or other components. In aircraft, extensive usage of fuses and circuit breakers helps prevent overloads by interrupting the electrical flow when an overload is detected.
Ensure proper maintenance on circuit breakers and fuses to avoid possible emergencies. For instance, damaged or worn-out components should be replaced, and functional checks should be performed regularly.
Maintaining System Integrity
The integrity of an aircraft’s electrical system, including its layout and components, is essential for safe operation. A critical aspect of this process involves the regular inspection and care of all components, such as:
- ATRs (Auxiliary Tension Rectifiers): These devices are used in some aircraft electrical systems to provide stable voltage between the engine starter motor and the rest of the electrical network. Regular inspection and maintenance help ensure their efficient performance.
- Engine Starter Motors: Ensuring that the motor operates effectively prevents possible delays in starting the engine and reduces strain on the aircraft’s electrical system.
- Wiring and Connectors: The condition of the wiring and connectors should be thoroughly checked for wear or damage since these can lead to short circuits, arcing, or other hazardous situations.
By continuously monitoring the condition of these components and promptly addressing any issues, pilots and maintenance personnel can help prevent electrical system failures, ensuring the overall safety of the aircraft and its occupants.
Footnotes
Diving into the world of aircraft electrical systems, our guide breaks down the essentials of DC, AC, and Combination systems in a way that’s easy to grasp.
From the simple yet effective DC setups in small planes to the high-powered AC systems in big jets, and the best-of-both-worlds approach with Combination systems, we’ve got it all covered.
Whether you’re just curious about how planes stay powered up or you’re deep into aviation geekery, this quick guide sheds light on the ingenious tech keeping aircraft soaring.
It’s a peek into the electrifying backbone of aviation, showing just how cool and crucial these systems are for flying high.